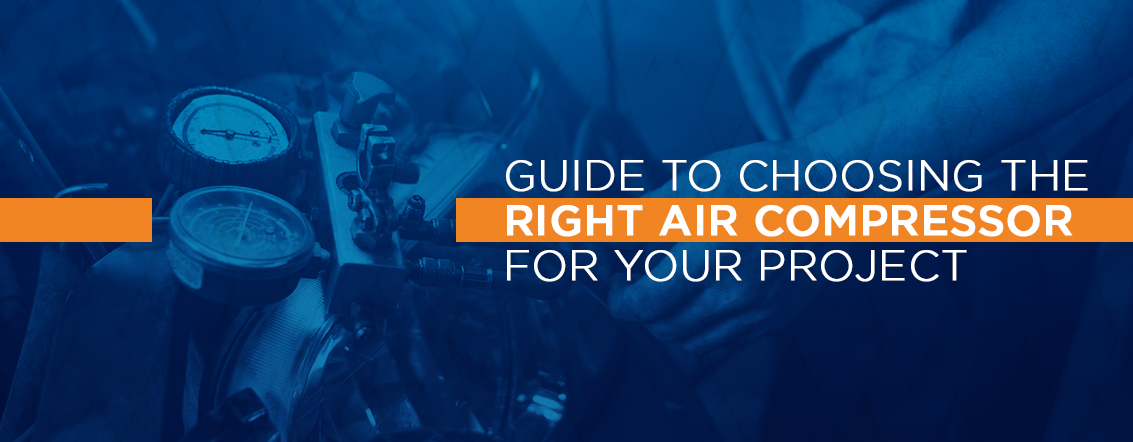
Air compressors are critical tools in the arsenal of homeowners, craftspeople and industrial workers alike, saving them time, offering better results and reducing operational costs. Compressed air tools can also reduce physical stress and fatigue from demanding or repetitive tasks while providing more professional results.
The tasks that air compressors help with run the gamut, from automotive repairs and metalwork to woodwork, carpentry and crafts. With so much versatility, choosing the right air compressor for your projects might seem daunting. However you use pneumatic tools, you’ll have to determine which air compressor is right for you. To help with that, we’ve compiled an air compressor selection guide to help you make sense of buying a compressor.
Reasons to Use an Air Compressor
An air compressor can be one of the most heavily-used pieces of equipment in many environments. Here are some of the reasons why.
1. All-Around Benefits
Out of all the different forms of energy in the world, compressed air is one of the most flexible and powerful options. Compared with the time and labor involved with traditional tools for construction, craft and automotive projects, tools that run on compressed air are a breeze in more ways than one. Using an air compressor gives you tools that:
- Have longer lifespans than conventional tools.
- Offer a range of different speeds.
- Offer torque control.
- Operate at lower temperatures and don’t produce heat during heavy usage.
- Don’t generate electrical shocks or pose a fire risk like many electrical tools.
- Don’t release toxins and are environmentally friendly.
- Generate superior power in proportion to their weight, offering easier operation than conventional tools.
- Have a low physical impact.
2. Better for Nailing Tasks
If your work consists of crafts, construction or carpentry, a nail gun could be the most critical tool in your toolbox. An air compressor is essential to run a nail gun without spending loads of cash. It all comes down to the costs of powering the nail gun. Those that run on batteries range from $200 to $500, while nailers that run on air compression are available for as low as $50. Additionally, pneumatic nail guns offer greater flexibility and are lighter in weight for easier portability. Furthermore, air pressure offers longer-lasting power than rechargeable batteries.
3. Speeds Up Painting
When it comes to work such as cabinet and furniture painting, an air-powered spray gun can help you get the job done in just a fraction of the time. You can also get a finer, more even finish on surfaces when you choose a spray gun over more traditional painting tools. Whether you do this to sell your projects or just as a personal hobby, an air-powered painter can make each piece of furniture look brand new.
4. Useful for DIY Car Repairs
You may be able to avoid the potentially high costs of car repair if you can maintain things yourself. Many smaller vehicle repairs, like tune-ups and filter changes, are easy to master and do yourself. Some of the most difficult parts of these tasks require getting bolts out of rusty spots and moving tight-fitting components. Where regular socket sets won’t do the trick, an air-powered ratchet tool can make quick work of the task.
5. More Efficient and Flexible
Compressed air tools offer efficiencies in time and money that simply can’t be beat by standard tools. Air compressors support an incredible range of tools and can help with a multitude of tasks. For example, if you’re cutting wood, you can use pneumatic blowing tools to clean up sawdust in a snap. If you’re adding cabinets or shelves to a home, an air-powered nailer can help you mount them in no time. Looking to hand your oldest kid’s tricycle down to your youngest? A spray-painting tool makes it easy to change the color to something they’d prefer.
Ultimately, air tools outlast and outperform their battery-run and cord-operated counterparts. There are fewer moving parts, and it is all powered by a single motor.
Determine Your Environment
One of the most significant factors that will play a role in choosing the right air compressor is your environment. Whatever type of work you do, your location and scope of work will influence which air compressor is right for you. Will you be moving the compressor often? Are you working in a large garage, outdoors in your driveway or yard or on a shop floor? Different types of compressors are available for these situations.
If you need to move the compressor, there are plenty of portable air compressor options. These machines are movable and can help you do everything from pump up equipment for a basketball game or power pneumatic tools at a construction site. Stationary air compressors are much more powerful. They’re bigger and heavier and offer much larger capacities. Typically, a stationary compressor is bolted into the ground.
There are two types of power options when it comes to buying an air compressor.
- Gas-powered air compressors: Gas engines allow you to power your air compressor in practically any setting, such as on location for a building construction project, where electrical sources aren’t easily accessible. A gas engine will add to the weight of items you’ll have to carry with you, but some wheelbarrow- and truck-mounted models can help minimize the stress of transportation. Generally, you should only use gas-powered compressors outdoors, where any fumes from the operation can escape.
- Electrically powered air compressors: Assuming you have steady access to an electrical outlet, these air compressors are best for indoor use. They can run on the standard voltage in your home or more powerful industrial outlets, depending on your needs.
Even for portable compressors, placement is an important consideration. Certain designs and styles can support different placement options. Typically, these won’t affect a compressor’s performance. They are more a matter of application, compressor size, floor space and portability.
Some of the most popular designs for portable air compressors include the following.
- Pancake compressors: These compressors are named after their round, flat bases that hold a 4- to 6-gallon tank. They are one of the most compact designs out there.
- Pontoon compressors: The Pontoon compressor has a long 2- to 3-gallon tank that is stored horizontally.
- Twin-stack compressors: The twin-stack compressor features two cylinders horizontally stacked on top of each other.
- Wheelbarrow compressors: A wheelbarrow compressor is built to be wheeled around and features dual tanks with handles.
Stationary compressors can be a little more versatile, depending on your individual needs.
Another necessary consideration is the amount of power you’ll need. Your projects and tools will put specific demands on any compressor, and some will be able to meet those demands better than others. Ask yourself the following questions as you move through the buying process.
1. What Amount of Pressure Will Your Projects Require?
The demands of your tool and your project will determine the capacity at which your compressor will need to operate. Review your arsenal of tools and determine which ones require the highest volume of air. This number will give you a rough idea of what to look for. Your compressor should offer an amount of pressure, usually measured in pounds per square inch (PSI), that exceeds this demand. The demands of your most powerful tools will also help you identify whether you need a single-stage or two-stage air compressor. Check out our guide on calculating your air demand if you need some help in this area.
A single-stage compressor works by compressing air directly into the tank, while a two-stage compressor pumps the air twice before reaching the final discharge pressure. If you’re working with many continuous-use tools, like sanders, or heavy-duty work, a two-stage compressor can offer better results. Many single-stage compressor pumps are capable of reaching 155 PSI, higher than their typical rating for cubic feet per minute (CFM), which is usually under 100 PSI. Two-stage air compressor pumps have a delivery of at least 175 PSI, with CFM ratings over 100 PSI.
For context, PSI measures the air stored in the tank. CFM refers to the amount of air that the compressor can deliver at different PSI levels. If you lower the PSI output, you increase the CFM. The more air a compressor can deliver, the more powerful tools it can run.
2. What Will Your Required Air Flow Be?
While CFM measures the air flow within a compressor, the amount of air that you harness is more accurately measured by the Actual Cubic Feet per Minute (ACFM). Before you decide on a particular compressor, check that its CFM is an accurate reflection of its ACFM.
3. How Much Horsepower Do Your Tools Need?
The horsepower of your compressor ultimately determines how much it is capable of generating. It runs in relation to the CFM rating. Watch out for machines with high horsepower but low levels of air flow. They tend to be short-lived if used regularly and aren’t the best option for professional use.
4. What Would Be Your Ideal Air Tank Size?
Once you identify your air demands, you can determine how large of an air tank you need. It should hold enough air to support your operation without being in the way. Keep in mind that vertical tanks don’t exceed 10HP.
5. What Is the Maximum Electrical Allowance at Your Base of Operations?
Using a compressor that surpasses your electrical allowance is a recipe for disaster. You’ll need to check what kind of voltage you have available. Many residential households have about 110 volts, which could support a machine of 3 HP at the most. Know your voltage in relation to the compressor’s horsepower before you make a purchase. You may want to consult with an electrician to ensure you’re getting the right size.
Our Testimonials
For Home Use
Even if you aren’t doing industrial-grade work, an air compressor is an excellent tool to have around the house that can save you plenty of calls to repair people or other workers. You can use it to fill your tires, sand wood and perform other odd jobs as they come up. An air compressor can help with home improvement and enable all of those projects you have in mind.
A single-stage air compressor is a good choice here, as you likely won’t need super heavy-duty tools. A portable option could help you as well since you can then move it around the house to the area you need it. You can probably get by with a smaller compressor if you’ll only be using it occasionally.
Some of the tasks you might want to use an air compressor for at home include:
- Spray painting
- Sanding
- Auto repair
- Inflating tires, balloons and sports balls
- Cleaning up debris like sawdust and grass clippings
For Industrial Use
When your work calls for heavy-duty, robust tools that can power even the most demanding pieces of equipment, an air compressor can easily become a necessity. Knowing how to pick an air compressor for industrial use can help you select the one that best fits your unique operational needs.
In industrial environments, you may have specific requirements to meet, so make sure you consider those before purchasing a compressor. For example, if you’re working with products like food or pharmaceuticals, you may need exceptionally clean air or air that doesn’t come in contact with oil. For the first issue, you’ll need a compressor that can accommodate air filters, which remove particulate and aerosol contaminants, and air dryers, which can help remove moisture. Installation may be more difficult as well, since you may want to wire it through to different areas in your facility. However, once you get it up and running, an air compressor can power a vast array of tools in an industrial environment.
For Craftspeople
If you create items like crafts, furniture and metalwork, a collection of professional pneumatic tools is essential. It can help you speed up your work and accomplish new tasks. You can build up this arsenal of tools within a home or garage at just a fraction of the cost, size and weight of the equipment setups in factories. With this powerful arsenal, you can grind, nail, spray, hammer and sandblast like a pro.
At Quincy Compressor, we offer some of the most efficient and compact air compressors on the market for this kind of work and home use. Our single-stage models are excellent choices that can help you get a wide variety of tasks done with ease. These options include:
- Q12120PQ: A portable 20-gallon horizontal tank with wheels, 115V, 2HP, 7.1 ACFM and 135 PSI
- Q12126VPQ: A portable 26-gallon vertical tank with wheels, 115V, 2HP, 7.1 ACFM and 135 PSI
- Q13160VQ: A stationary 60-gallon tank with 230V, 3.5HP, 12.4 ACFM and 135 PSI
For a two-stage compressor, look no further than the QT 5-15 HP Standard Duty Two Stage models.
Manufacturing and oil and gas are some of the top users of compressed air. However, many other businesses use them, from agriculture and energy exploration to pharmaceuticals and dry cleaning. Air compressors are extremely versatile. Here are just a few of the tasks you can use them for:
- Operating pneumatic material handling equipment
- Cutting and welding tools
- Sandblasting and finishing metal
- Ejecting pieces from production molds
- Spraying crops
- Efficiently performing basic tasks like driving screws and turning nuts
- Bottling, packaging and palleting products
- Cooling and freezing products
Air Compressor Features and Project Tool Attachments
With so many different options, it stands to reason that you have a variety of features and attachments to consider. Finding the best air compressor for your air tools and your project depends on which ones you’ll be using. Here are some of the common tools you’ll find used with an air compressor and the requirements that come with them.
- Angle disc grinders: This tool is popular among builders and metalworkers and helps to remove extraneous material from a construction piece. Workers might use them with blades, brush wheels, buffing pads or grinding discs in addition to sanding discs. Air-powered angle grinders generally require 6 CFM.
- Die grinder: A die grinder is a rotary tool used on wood, plastic and metal to sand, polish and grind rough edges and surfaces. It is popular among sculptors, welders and millwrights and serves as a handy engraving and contouring tool. Pneumatically driven die grinders typically require 8 CFM.
- Random orbit sander: This type of power sander uses a randomly orbiting blade, which means that it spins in multiple directions. Many craftspeople and furniture makers prefer it to orbital sanders because it provides a smoother finish and no swirl marks. This result is due to the tool’s non-constant motion, which never retreads the same path on a surface. The random orbit sander usually requires 6 CFM.
- Grease gun: Many workshops use grease guns for the precise application of lubricants on machine parts. Pneumatic grease guns use compressed air to force the thick grease through the opening and onto machine joints and other parts that require lubrication. Generally, grease guns require 4 CFM.
- Impact wrench: The impact wrench is an air-powered socket tool that many mechanics use in auto repair work, where it has eclipsed its electric counterpart. It is also used in building construction, machine maintenance, product assembly and various other heavy-duty applications. The best air compressor for an impact wrench is one that can reach at least 5 CFM for a 1/2-inch wrench and 7 CFM for a 3/4-inch wrench.
- Air hammer: An air hammer is a pneumatic tool that craftspeople use to break up objects and carve materials into form. The air hammer can accommodate a variety of tools, such as joint separators, exhaust pipe cutters, shock absorbers, rubber bushing splitters and tie-rods. It can stretch, shrink and smooth a wide range of metals, making it great for everything from thin aluminum to 10-gauge steel. When choosing an air compressor for an air hammer, look for one with at least 4 CFM.
- Sandblaster: Builders and mechanics often use sandblasters to peel away corrosive deposits like rust, grease and old paint from other materials. A 3-gallon sandblaster generally requires 4 CFM.
Here are a few other tools and their CFM requirements.
- Air drill: 4 CFM
- Butterfly impact: 3 CFM
- Cut-off tool: 4 CFM
- High-speed grinder, 5-inch: 4 CFM
- Ratchet, quarter-inch: 3 CFM
Which Features Would be Essential for Your Type of Work?
We’ve already mentioned the use of filters and air dryers, but a compressor can have other features critical for your kind of work. The general design of a compressor can support operations that are intensive or require lightweight tools. Some popular features include:
- Thermal Protection: If an overload occurs, thermal protection cuts the motor, preventing damage to the machine.
- Exhaust adjustment: In an enclosed work environment, exhaust can be problematic. With exhaust adjustment features, you can funnel the exhaust in another direction.
- Multiple couplers: If you use a variety of tools with your compressor, couplers allow you to keep them attached simultaneously and switch between them as needed.
If you work outdoors, look for things like a cast-iron body, which can make a compressor more durable in harsh weather conditions like rain and snow, and stainless steel valves, which help prevent corrosion. Consider the type of work you do and what features will be beneficial.
Partner With Quincy Compressor to Improve Your Efficiency
Hopefully, this air compressor buyer’s guide has helped you determine what kind of air compressor you need for your project. You’ll want one that fits your location, tools, power availability and any other needs.
For more than a century, builders, mechanics and craftspeople around the world have turned to Quincy for a wide range of air compressors, tools and accessories. Within our vast inventory are machines suited for operations large and small, including the QR-25 reciprocating air compressor unit and the more heavy-duty rotary screw air compressor models like those in the QGS series.
Our customers get unbeatable deals on some of the most durable, high-quality air compressors on the market. They also receive 24/7 customer support and long-lasting warranties. Ready to invest in a product that can reduce hours of work into minutes with just a fraction of the effort? Browse our compressors or contact a representative today. You can even read through our white pages for more information on our compressors.