Compressed Air Use in Standard Oil and Gas Industries
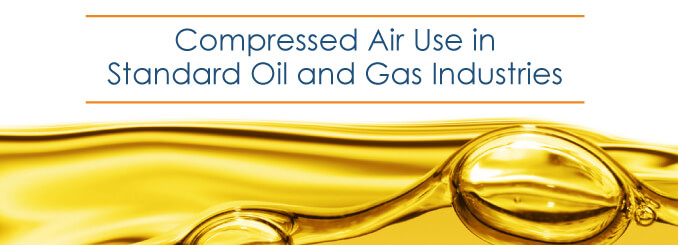
For centuries, the only way to harness the mineral and fuel-rich materials of the planet was to use an old-fashioned shovel. Today, technology has improved exponentially, allowing not only for easier access, but larger yields of the Earth’s great natural resources.
One of the most precious commodities in today’s world is petroleum, a word which is used to describe naturally occurring crude oil, as well as refined petroleum products. Crude oil is a fossil fuel that is comprised of the remnants of ancient algae and zooplankton, which were subjected to intense pressures and heat deep within the earth over millions of years.
Oil drilling is the most common method of siphoning this rich resource, but in some cases, naturally occurring oil springs have been found. The location of oil is highly dependent on the geological makeup of the region, but drilling is now a common practice across nearly every continent in the world. Through refinement and distillation, a vast number of products are created from the raw material.
From the many plastics that have greatly improved manufacturing capabilities, and the consumer products used throughout our homes, to the gasoline we use to power our automobiles, oil is a vital necessity in the modern world.
Crude oil used for the creation of fuel has powered human progress through the early industrial age, and has long been a source of booming economic growth for the world’s oil-rich countries. Even other fuels like kerosene are derivative of this hydrocarbon.
Petroleum is in such high demand in today’s world, that it’s estimated that nearly 95 million barrels are utilized each day worldwide. Without oil, modern society would not have been made possible. In part, the advancement of technology has been dependent on oil, while harnessing oil has been dependent on increasingly efficient technologies.
From large drilling equipment used in offshore oil rigs to essential air and gas compressors, the modern oil and gas industry depends on durable, high-quality machinery to siphon crude oil from the Earth. In addition, specialized equipment is also needed for the refinement and distillation processes used to create gasoline, plastics, asphalt and other essential petroleum-based products.
A Brief History of Oil Drilling Technologies
While drilling technologies have greatly advanced over the past century, many other aspects of the industry have also grown into what we see today. In the early days, drilling had already been established long before oil or natural gas was harnessed for any useful purpose. Early drilling was used to search for a more important natural resource than oil: water. The quest for clean drinking water dwelling deep below the surface set the stage for some of the earliest forms of drilling technologies.
Early drillers developed a system that utilized the tension of a bent tree with a spring pole to dig a hole into the ground in their pursuit of a new well. In many ancient historical recordings, this method was used, and is still used today in some parts of the world. The spring pole and chisel were invaluable, and practical tools to find life sustaining resources. One of the most well-known accounts came in 1802, when West Virginia salt brine drillers managed to reach a depth of 58 feet with a spring pole. Oil wasn’t considered very useful to the brine drillers, and acted as a nuisance if it contaminated the work site.
With the advent of steam power, and more advanced forms of mechanical engineering, drilling became a much easier and more efficient task. In Pennsylvania, the entrepreneurial spirit of several businessmen started the modern oil industry after they figured out they could sell what was often considered a detriment for those seeking water and brine.
Oil was used medicinally and as a lubricant, despite its foul stench. The Ruffner brothers and Samuel Kier of Tarentum, Pennsylvania, began to market by patenting a variety of oil-based medicines and lubrication products. This simple act gave birth to a widely popular industry, and cemented oil’s place as a useful commodity.
By the early 1900s, oil drilling had advanced and with it, the use of more complex equipment for extraction. Rotary drilling became a common practice in oil-rich areas like Texas, and opted for a hollow drill stem that used fluid to push broken rocks and debris from the borehole as it was re-circulated. This was much more efficient than the heavy cable-tool rig systems that predated it. Rotary drilling rigs soon became the best way to drill for oil, which is still reflected in much of today’s modern drilling machinery.
The record depth for a cable-tool rig is 11,145 feet, but Russia reached a depth of 40,000 feet within ten years of using a rotary system.
From there, several advancements in drill bits and rotary technologies were made, creating the systems we see today, which can reach to great depths and provide much faster methods for extraction. One technological advancement that has also contributed to the industry was the use of air and gas compressor systems.
Within the past 10 years, oil fields would often flare petroleum gas, which was the result of treating crude oil before it was transported in a pipeline. However, new regulations demanded that 95 percent of petroleum gas must be processed, requiring it to be compressed. In order to do so, compressors were needed at the oil fields. Commonly, reciprocating gas engine-driven compressor systems were employed while being fueled with the transported gas.
In addition, compressors are often used in oil fields for gas re-injection for maintaining reservoir pressures. By using a series of compressors, gas or, in some cases, air, can be used for re-injection. Both centrifugal air compressors, which are often the initial compression sources, as well as reciprocating compressor systems, are used to meet required pressures.
Because well flow and reservoir pressures slowly decrease over a period of time, compressors are often used to maintain or increase gas flow into a pipeline system, as well. Depending on the demand, or application, both centrifugal or reciprocating compressor systems can be useful.
Types of Air Compressors Used in the Oil and Gas Industry
As mentioned, both centrifugal and reciprocating compressors are used in the oil and gas industry. Below, we will take a look at these two types of compressor models, and their specifications:
Reciprocating Air Compressor
A reciprocating air compressor system operates through a crankshaft-driven piston and cylinder, which is used to compress the air. There are both single- and two-stage designs. In a single-stage, a solitary reciprocating piston works by drawing air into the cylinder. In a single stroke, this creates the compression, which is then sent to a storage tank.
In addition, two-stage reciprocating compressors include an additional step where a smaller piston is used. This can produce an even higher pressure if needed for certain applications.
Centrifugal Compressor
Centrifugal compressors are different than reciprocating models, as they depend on the continuous flow of fluid through a rotor. Depending on the type, they may be a single-stage or multi-stage compressor, and are driven by large gas turbines. Unlike reciprocating compressors, centrifugal compressors are often reserved for the largest oil and gas operations and require thousands of horsepower.
Gas Compressors
Gas compressors are used in a variety of important tasks in the oil extraction, transportation and refinement processes. As with natural gas, many compressors in these industries require a compressor that can increase the pressure of a gas by reducing volume. As with other reciprocating models, gas instead of air is forced into a cylinder and then pushed out through discharge valves.
Rotary screw models are also used, and operate through the use of matching helical screws. As the screws rotate, air moves through the threads.
These types of compressor systems are used for the compression of gases in refineries and processing facilities. In addition, compressors are used to power tools and machinery in plants as well as in the transportation of products and materials through pipelines.
At Quincy, we are experienced in the manufacturing and design of high-quality gas compressors that offer the best in terms of performance for both our rotary and reciprocating models.
Take a look at a few of our recommended models of reciprocating and gas compressors below:
Depending on the application your operation demands, air and gas compressor requirements will vary. For more specific information on what compressor would best serve you, contact Quincy directly. Our qualified and dedicated team will provide you with the necessary information, and help you find a distributor near you.
Common Compressor Applications in the Oil and Gas Industries
Operations both large and small utilize compressed air systems for a variety of purposes in their operations. Everything from pneumatic tools to pipeline transportation can benefit from a compressor system. Take a look at some of the most common applications compressors are used for:
- Petroleum Refining — By boosting the pressure of processed gas, a catalytic reaction used in the refining process will occur.
- Petrochemical Synthesis — Petrochemicals such as methanol, ammonia, ethylene, ethylene glycol and urea often rely on a specific pressurization of air and gas in the manufacturing processes.
- Pipeline transportation — Utilizing gas and compressed air is common in transporting gas through pipelines. Pressures need to be maintained, which requires some form of compressor system to work correctly.
- Gas injection — Increasing gas pressures and injecting oil layers can help promote the recovery of crude oil.
In addition, air pressure is often used for the transportation of liquids, pressurization of tanks, cooling, molding of petroleum products like plastics, as well as the synthesis of various petrochemicals.
The Future of Air Compressors in Oil and Gas
As consumer needs for fossil fuels continue to increase with the global population, the world will continue to depend on oil as an essential natural resource, despite developments in alternative energy sources. The increased demand for oil and oil-based products throughout the ages has promoted astonishing advancements in drilling technologies and in the refinement processes.
As a result, air and gas compressors have become vital for delivering the necessary pressure levels for these operations, and their demand is expected to continue to grow within the oil and gas industry over the next several years.
Analysts predict the industry will grow 7.2 percent between now and 2020. Emerging markets for oil will also play a role, as new areas are drilled and growing countries begin their own exploration for more natural resources. China has already seen a drastic boom in both oil and gas demand within the past five years, and will play a large role in future market growth. Because China has grown into one of the largest energy consumers in the world, they have now surpassed the United States as the largest importer of crude oil and petroleum-based products.
The increase in market demand for these products has also increased the demand for the equipment needed in the extraction and refinement of crude oil. While China sees lower production costs when it comes to developing products, the raw materials needed for manufacturing are also affecting the global air compressor market. Important materials like aluminum and steel are used for the creation of air compressor components, but as demand increases, prices for the raw materials will also fluctuate.
In addition, next-generation air compressors will play a prominent role in the continued growth of the market, as vendors make improvements and add new innovations to their products. Innovations like increased speed and reduced energy requirements will help air compressor manufacturers maintain a competitive edge in the coming years.
Air compressors that are designed to withstand the harsh environments of drilling sites and maintain peak efficiency for the long-run are important. While the energy demands for compressor systems are high, proper inspection and routine maintenance can drastically reduce energy costs and increase operating efficiency.
How Can Quincy Help Me?
At Quincy, we offer high-quality products that are built tough. Our products are engineered to last for decades and are built with durability in mind. For heavy-duty use in diverse environments, Quincy compressors can deliver systems that work day in and day out. Whether you’re working onshore, or off, Quincy delivers reliable products specially designed for the demands of the oil and gas industries.
We specialize in air compressors for drilling rigs, pipeline operations, petroleum refineries and more.
Drilling rigs and stationary platforms in open waters can’t afford unreliable air or gas compressors. Productivity can come to a halt when salt and humidity begin to compromise the performance of an air compressor on a drilling rig, where help may be miles away. At Quincy, we have exceptional quality control processes to make sure your operation flourishes. In addition, we offer some of the best warranties in the industry.
For more specific information regarding the ideal compressor, or the compressor line of interest for your operation, contact us directly.